To reduce the operating costs of the Speedmullor, Simpson conducted a study on different materials to determine what material would provide the optimal combination of cost and performance to withstand the highly abrasive application of mixing molding sand in foundries. Multiple trials were conducted with different alloys and the results proved that a redesigned, six-piece cast Ni-Hard bottom bowl provided the best overall solution for cost, ease of replacement and wear resistance.
What are the Differences between Gray Iron and Ni-Hard?
The difference between gray iron and Ni-Hard bottom bowl liners comes from the mechanical properties coming from the metallurgy of those two metals. Gray iron is a carbon supersaturated ferrous matrix where the free carbon is suspended in the form of graphite flakes. Ni-Hard is a high Nickel-Chromium-Carbon Alloy which does not have graphite flakes like gray iron does but instead has chromium-iron carbides.
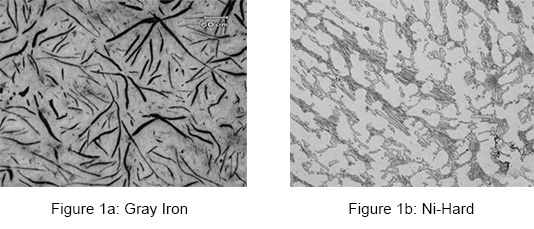
Elements like chromium and nickel add to the hardness and corrosion resistance of Ni-Hard, ultimately giving it 400-500% improved wear resistance when compared to Gray Iron. Ni-Hard is commonly specified for high abrasive applications in the cement, concrete, gravel, rock, metallic mineral and sand mining industries.
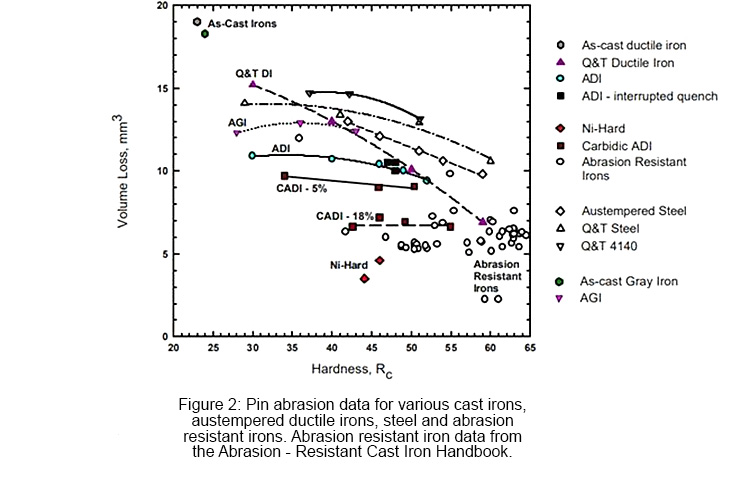
Simpson Ni-Hard Bottom Bowl Liners Are Exclusively Made for the Speedmullor
Once Ni-Hard was identified as the optimal metallurgy Simpson worked with a partner foundry to further improve the characteristics of the particular Ni-Hard we would select for the bottom bowl liner. Ni-Hard comes in various types based on metallurgy: Ni-Hard 1, Ni-Hard 2, Ni-Hard 3 and Ni-Hard 4. Working closely with the foundry, Simpson chose a unique, improved formulation of the typical Ni-Hard 4 for its higher hardness and higher fracture resistance due to its higher chrome and nickel content. This unique Ni-Hard 4 alloy provided an additional 20-25% improvement in hardness and wear resistance when compared to a generic Ni-Hard Type 4.
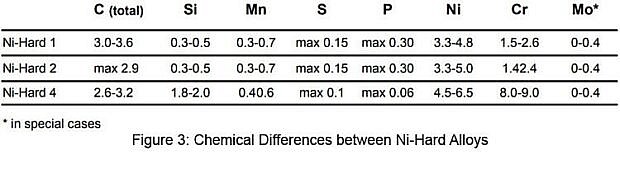
Extended Bottom Bowl Wear Life
Assuming that all conditions are the same, life expectancy of the Ni-Hard bottom bowl liner is at least four to five times longer than a standard gray iron bottom bowl liner. The cost benefit of the Ni-Hard bottom is better in higher production foundries. A high production foundry operating 20 hours per day for 260 days per year would consume 6,000 operating hours in about 1.2 years of production which would require a new bottom bowl to be purchased and installed relatively frequently. That same foundry using a Ni-Hard bottom bowl with a life of 30,000 hours wouldn’t have to change the bottom bowl for 5.7 years. The savings in reduced bottom bowl purchases and fewer maintenance events to change a worn bowl far exceeds the additional cost of the Ni-Hard bottom bowl and significantly reduces the total cost of operation for the Speedmullor.
Ease Of Installation
To make the storage, movement and installation of the bottom bowl easier the Ni-Hard bottom bowl liner comes in 6 pieces compared to the standard 2 piece gray iron bottom bowl liner. On the most common model 100B Speedmullor one of the six sections of the Ni-Hard bottom bowl liner weighs 420 lbs. / 190 kg. compared to one of the two sections of the gray iron bottom bowl which weighs 1,250 lbs / 565 kg.
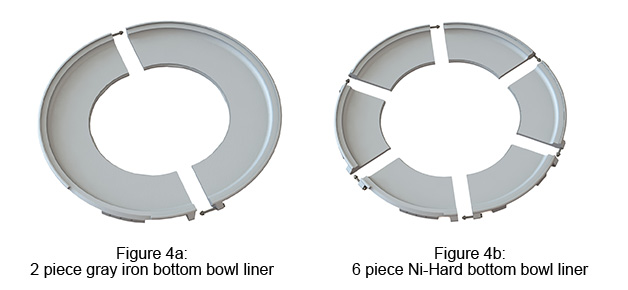
Improved Muller Performance
Since the Ni-Hard bottom bowl retains its original shape much longer it significantly reduces the wearing and consumption of plows. The plows retain their original shape much longer and maintain their performance in sand movement into the mulling zone. Since both the bottom bowl and plows retain their shape longer less maintenance is required to clean the muller bottom and adjust the plows.